CO2 Refrigeration System: How It Works
In a world where climate change is already an urgent reality, the way we approach everyday technologies, especially those related to cooling and refrigeration, is changing. One such advancement in the world of refrigeration technology is the CO2 Refrigeration System. Undoubtedly, a revolutionary approach that is reshaping the way we think about cooling processes.
Unlike traditional refrigeration systems that rely on harmful refrigerants, transcritical CO2 systems utilize carbon dioxide, a natural and environmentally friendly substance. However, what sets this system apart, and why is it gaining traction in commercial and industrial applications worldwide?
In this blog post, we demystify the complexities surrounding these systems, shedding light on their components and functions. We will understand the science behind transcritical CO2 refrigeration and explore its practical benefits. From supermarkets searching for eco-conscious refrigeration solutions to industrial giants minimizing their carbon footprint, transcritical CO2 systems have become synonymous with sustainable cooling.
Essential Components
At the heart of every CO2 Refrigeration System lies a series of meticulously designed components, each with a specific function and purpose. From the compressor, where the refrigerant’s journey begins, to the high-pressure valve, the heart of the technology, these components work together seamlessly, creating a cycle that ensures efficient cooling while minimizing environmental impact.
In this infographic, we will be looking into a CO2 booster system, considering cooling and freezing operations. We will break down the system into its fundamental parts: the compressor, gas cooler/condenser, high pressure valve, gas bypass valve and evaporator.
1) The compressor
Serves as the powerhouse of the refrigeration system. Basically, its primary function is to compress the low-pressure CO2 gas, elevating both its pressure and temperature. This compressed gas, now in a high-energy state, is the driving force that fuels the entire refrigeration cycle.
In a booster system, two suction groups are feeding the compressors:
– Medium-stage compressors process the medium temperature (MT) evaporation of the cooling loads, typically running around 28 bar, which corresponds to – 10 °C;
– Low-stage compressors process the low temperature (LT) evaporation of the freezing loads, typically running around 13 bar, which corresponds to – 32 °C.
2) The gas cooler/condenser
Inside the condenser, the high-pressure, high-temperature CO2 gas is transformed. In this component, heat is released, causing the gas to transition into a liquid state. This phase change is crucial, as it signifies the system’s ability to shed the absorbed heat, making the environment cooler.
In a CO2 booster system, this equipment will work as a condenser when operating in subcritical mode and as a gas cooler, in the transcritical mode.
3) The expansion valve
Its function is to regulate the flow of the high-pressure liquid CO2, causing it to undergo a rapid pressure drop. This drop results in a substantial decrease in temperature, turning the liquid into a mixture of liquid and vapor.
In the booster system that we are analysing, there are 4 expansion valves:
– High-pressure valve: controls the pressure at the gas cooler/condenser, decreasing the pressure from the high-pressure side (90 bar) to the receiver pressure (38 bar);
– Flashgas bypass valve: controls the pressure at the receiver, decreasing the pressure down to the 38 bar of MT suction pressure;
– MT expansion valve: responsible for the expansion of the liquid on the receiver from 38 to 27 bar;
– LT expansion valve: responsible for the expansion of the liquid on the receiver from 38 to 13 bar.
4) The evaporator
Here, the low-pressure and low-temperature CO2 liquid-vapor mixture absorbs heat from its surroundings. This absorption causes the refrigerant to evaporate, transforming it back into a low-pressure gas. The cycle is complete, and the space around the evaporator becomes cooler. As mentioned before, in this booster system there are the MT evaporators and the LT evaporators.
In conclusion, each component is a fundamental force driving efficient and sustainable cooling solutions.
Advantages of CO2 Refrigeration System
These systems utilize carbon dioxide (CO2) as a natural refrigerant and come with a multitude of advantages that not only benefit businesses, such as supermarkets, and industries, but also contribute significantly to environmental conservation. These are the advantages of a CO2 Refrigeration System:
1) Environmental Sustainability
CO2 helps mitigate significantly the greenhouse effect and minimizes climate change concerns.
A CO2 Refrigeration System does not contribute to the depletion of the Earth’s ozone layer, making it environmentally friendly and compliant with international environmental agreements. Compared to traditional refrigerants, CO2 has a significantly lower Global Warming Potential (GWP), reducing its impact on global warming.
2) Energy Efficiency
What’s more, CO2 systems can achieve optimal cooling effects while consuming minimal energy.
It boasts high Coefficient of Performance (COP) values, resulting in reduced electricity bills and operational costs for businesses. CO2 systems can easily adapt to variable speeds based on demand. This adaptability ensures that the system operates efficiently even during fluctuating cooling needs, optimizing energy usage and reducing wastage.
3) Safety and Non-Toxicity
CO2 ensures the safety of both workers and consumers.
Unlike some traditional refrigerants, CO2 poses no health risks, making it a reliable choice for various applications, including food and beverage industries. CO2 is non-flammable under normal conditions, enhancing the safety of these systems. This characteristic eliminates the risk of fire hazards associated with certain other refrigerants.
4) Operational Versatility
The CO2 system’s versatility allows for customized cooling solutions tailored to specific industry requirements.
It finds applications in diverse sectors, including supermarkets, food processing units, and industrial facilities. Explore our CO2 installations and find out more about our Case Studies. CO2 systems exhibit consistent performance across a wide range of temperatures, making them suitable for both tropical regions and cold climates. Their reliability in varied conditions enhances their applicability globally.
5) Regulatory Compliance and Future Proofing
Ensure businesses’ compliance with evolving environmental mandates.
CO2 refrigeration systems align with international environmental regulations and standards. By adopting CO2 refrigeration technology, businesses future-proof their investments. With the global shift towards sustainable practices, CO2 systems provide a long-term, eco-friendly solution, safeguarding businesses against regulatory changes and market demands.
Conclusion
Shortly, what emerges is a profound understanding of a technology that not only cools spaces but also plays a pivotal role in shaping a sustainable future. CO2 Refrigeration System’s advantages extend beyond mere efficiency, encompassing environmental stewardship, safety, and adaptability. Businesses adopting these low-GWP systems not only optimize their operations, but also contribute significantly to the preservation of our planet.
With each technological advancement, we inch closer to a world where cooling systems no longer deplete the ozone layer or contribute to global warming. The future of sustainable cooling is here, and it’s undeniably green, efficient, and promising. Interested in finding out the right CO2 Refrigeration System? Discover our products and our applications range.
Building Connections
On LinkedIn
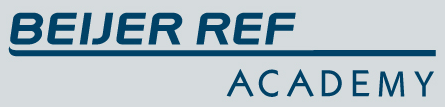
Become a CO² Specialist
Beijer Ref Academy will offer technicians and installers the opportunity to learn how to operate CO2 refrigeration systems in different configurations.